How do you know your engine or the engine-driven machine moves properly? Visual checks are neither practicable nor inefficient in this case. However, a special mechanism, such as a position encoder, monitoring moves and transmitting the results to a control device is just the right solution. From the feedback, the user not only understands what is right and what is wrong about motion in an application, but gets a hint on where and how to fix trouble, if any.
Why positioning data is important
When coupled to a motor, a position encoder aims at bringing the rotor and stator operation in sync with input amperage. The transducer tracks carefully how the two components change their positions to spot the precise moment for applying sufficient current to maximize torque output. Typically, its feedback comprises velocity and positioning data—linear or angular, depending on whether measured movements are along a straight line or in a circumferential direction.
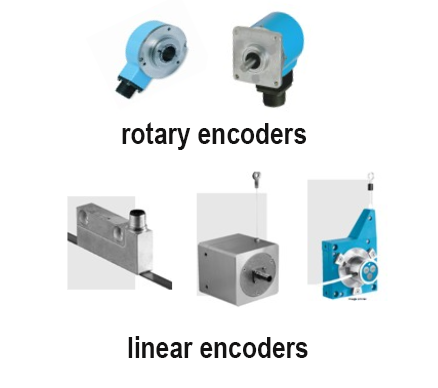
In a solution where accuracy is key, a position encoder is a critical component. Without the device, users are clueless whether the resulting propulsion is in compliance with the commanded parameters or deviates in an abnormal way. In the circumstances, errors are inevitable, leading to high failure rates, irreparable damages to the equipment, or even accidents and injuries.
Where safety is a concern, the sensing mechanism is a stronghold to rely on for predictability of motor behaviour, which is highly variable depending on loads. Feedback from a position encoder shows how an actuator handles a load moving along a trajectory and how an application makes it through work cycles with specific motion settings.
Repeatability properties of a driven machine—i.e., the ability to reproduce preset motion consistently—depend on availability of real-time position and velocity data. Absolute encoders totally support the capability, empowering users with fast and precise command response.
What affects encoder accuracy
Though contributing greatly to precision of movements, a feedback device alone will not necessarily fix you up with motion matching exactly the desired control input. All the more, position encoder accuracy is at risk when the following factors come into play:
- Mechanical slipping of components in a driven machine or in the actuation mechanism proper
- Backlash, or mechanical play, generated by transducer bearings (which is, to be fair, rarely encountered in modern models) or a gearing mechanism
- Ambient conditions, such as temperature, humidity, dust or particulate contamination, as well as electromagnetic interference
- Characteristics of the control device communicating with the position feedback device, including their general compatibility
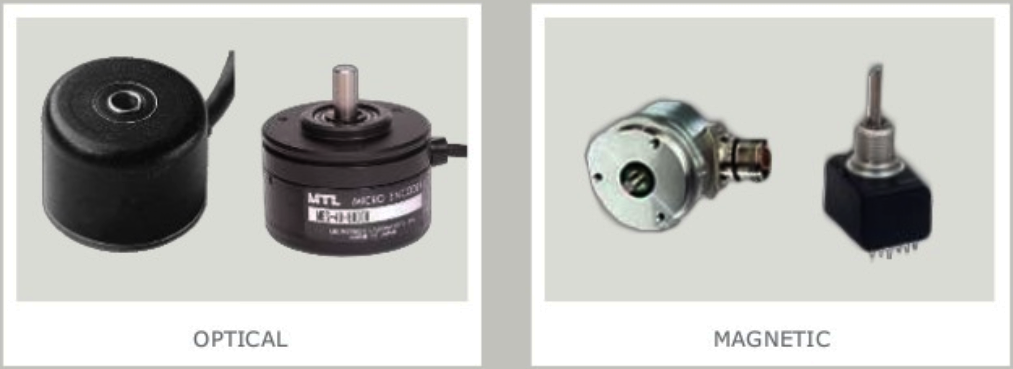
Essentially, mitigation of the risk factors resolves into selecting a proper encoder type. Options are numerous: sensors delivering absolute or incremental data, based on magnetic or optical measuring technology, or even alternative mechanisms—e.g., resolvers.
Which position encoder is better
The short answer—it depends. The detailed response goes like this: you have to count in the specifics of your application, the output you want to get, and the above factors that influence encoder accuracy. The comparison tables below are there to help you with initial assessments.
Magnetic or optical technology
Magnetic encoder
- Highly immune to most aggressive agents, including dust, moist, oil, except for magnetic debris or powder.
- Handle exposure to shock, vibration, suddenly dropping or rising temperature with almost-zero impact on performance.
- Robust body makes additional sealing or reinforcement arrangements superfluous.
- Boasts mechanical simplicity, durability, and compact dimensions; relatively low-cost sensing technology.
Optics-based position sensor
- Penetration of particulates and liquids into the transducer body can affect significantly its readings. Outdoor use is hardly possible, but performs superbly in strong magnetic fields.
- Ambient temperature variations can cause condensation on optical elements, resulting in impaired measurement capacity.
- Employs a more complex and expensive optics-based working principle, but offers high resolution and responsiveness.
Non-relative or relative response
Absolute measurements
- Each position is an absolute value correlating with a unique error-checked binary code. The Gray encoding method minimizes error down to 0.5 bit, because each subsequent reading differs from the preceding value by one bit only.
- Capable of delivering real-time motion feedback, available immediately at startup or after a power outage.
- The encoder shaft doesn’t have to rotate for the user to be able to read actuator positions.
- The user has no access to motion data when the device goes offline. With the great real-time communication capability, absolute sensors save extensive amounts of processing power when one needs to handle large data volumes.
- Enabled by a serial connection, the device is resistant to electrical noise effects.
Measurements in incremental steps
- Measurements represent incremental shaft displacements relative to a reference. To determine true, non-relative positions, additional calculations and arrangements (e.g., to count total steps) are essential.
- Decoding of the quadrature output demands signal processing in external circuitry. In addition, a homing or post-outage recovery procedure is needed to establish a measurement reference. The factors lead to extra latency in determining positions with incremental encoders.
- Monitoring multiple transducers requires complex data processing arrangements and significant resources to interpret acquired information.
- More sensitive to electrical noise than absolute counterparts.
The alternative of using a resolver
Similarly to encoders, resolvers employ the mechanical-to-electrical conversion principle to determine positions of a motor or any other mechanism. However, differences in both design and operation are substantial:
Resolvers
- Boast super robust casing and resilience to shock, vibration, and other kinds of environmental impacts. This enables utilization under tough conditions, but makes them bulky and heavy.
- Integration is a challenge: the user has to provide separate excitation and data processing lines. Upgrades are complicated, demanding replacement of numerous components and time-consuming adjustments.
- Feature superior resolution, but inferior accuracy (50 to 3 arcmin) as compared to encoders.
- Limited speed ranges.
Encoders
- Demonstrate superior performance when used with machines that accelerate and decelerate quickly. High external loads and temperatures deteriorate operational efficiency.
- Light weight and compact dimensions enable versatile mounting options. Support of digital communication warranties compatibility with most modern control systems. Upgrading is as easy as replacing the sensing element and updating the software.
- Ensure accuracy of up to 3 arcseconds.
- Remain functional over a wide velocity span.
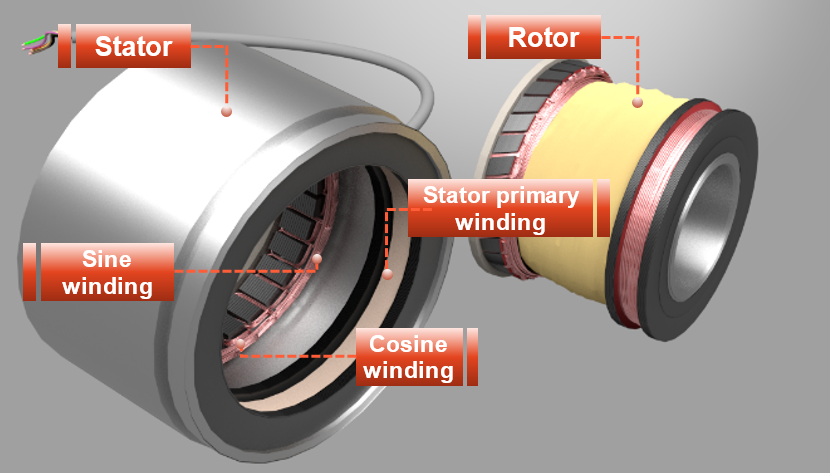
In other words, resolvers are a preferred option in harsh environments, where rugged design is more critical than precision or integration issues. Encoders are a better choice to read positions in those applications where accuracy is foremost or where a measured machine starts or stops rapidly and frequently.
Reading RDrive positions
In the RDrive series of high-torque servo motors, Rozum Robotics has implemented the following motion feedback system:
- A couple of embedded absolute encoders communicate true servo positions to a built-in controller via a serial BiSS connection. Located both at the rotor and the output shaft, the transducers compensate any measurement inconsistencies resulting from gearing.
- With absolute response, users have both online and offline access to ultra-precise real-time drive parameters, such as rotation angles, velocity, movement direction, etc. Measurement accuracy is 2.5 arcsec and resolution—19 bit.
- Sensing is based on the magnetic technology, due to which the transducers boast remarkable reliability and durability. An extra advantage is their immunity to adverse effects, including dust accumulation, abnormal temperatures, oscillation, etc.
It is also worth mentioning that the devices are already matched against the other components of the RDrive closed-loop control circuit. So, you can easily skip the tedious and costly integration design and servicing parts.